
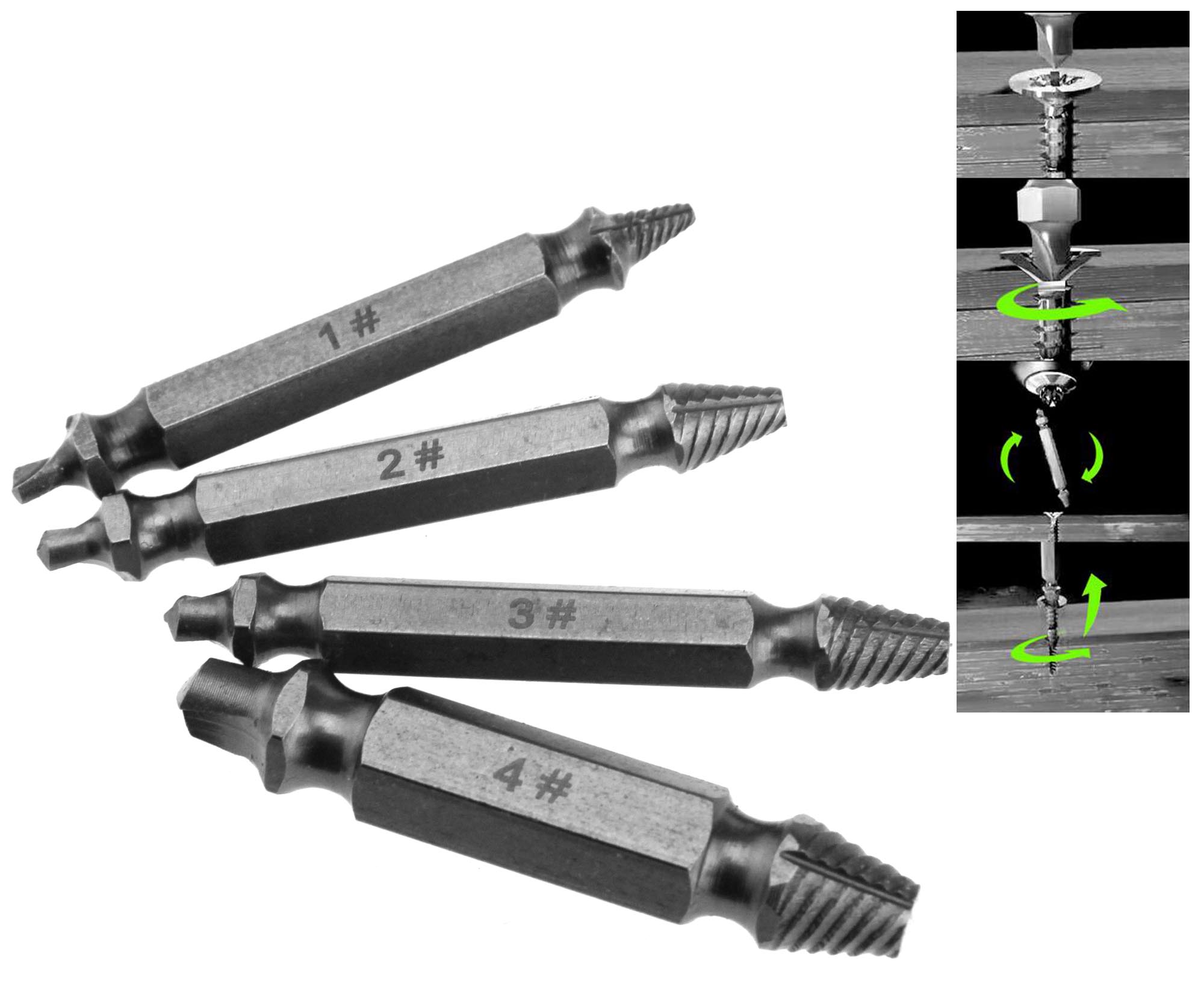
Here is my video taking you through how to use a screw extractor step-by-step: I once used an easy out kit to remove a snapped bolt on the undercarriage of a Chinook Helicopter, 300 miles North of the Arctic Circle (This was nothing to do with me over-tightening the bolt this time it was the -25 degrees Celcius temperatures which were placing every component under stress and equipment failures were common.) When used correctly they are simple and effective. I have been using screw extractor sets for many years after first learning about them during my apprenticeship as a mechanical technician in the Royal Air Force, where I served as a technician on aircraft for 7.5 years. So off the cylinder head came again (oh what fun!).

The torque wrench failed to ‘break’ at the desired torque, and as a result one of the head bolts snapped in between the cylinder head and the engine block. Unfortunately, I chose to use a very cheap torque wrench to tighten the head bolts up to the required 70 N m. I had already done this once before, so I wasn’t too concerned about the job. The backstory behind this post and my video is this: I was working on an engine and after completing the work the time came for me to refit the cylinder head to the engine block.

Place the screw extractor in the hole, and hit it once with a hammer.If you have chosen a larger diameter screw extractor then start off using a small drill bit and then progressively open out the pilot hole you made until you have appropriately sized hole.) The larger you go the less likely it is that you will snap the screw extractor when you apply torque. Using a small diameter drill, drill down into the broken fastener, being careful to stay centred and going deep enough to avoid the screw extractor bottoming out in the hole (The size of screw extractor to use depends on the size of the fastener, and the estimated torque required to break it free.Hold the centre punch in position and hit once with a hammer. Pick up the mark you just made with a centre punch.Mark the centre with an engineers scriber.Make a flat surface in the middle of the snapped portion using a hand file, angle grinder, dremel tool or similar.Here are the steps required to use a screw extractor set: I made a step-by-step video to show you exactly how you can use an easy out to remove a fastener on which the head has snapped off. Once you feel the extractor take hold, continue turning counterclockwise and pull to completely remove the stripped or broken screw.In this post I show you exactly how to use a screw extractor set to remove a broken head bolt from an engine. As you turn the screw extractor, its threads will draw it in until it bites into the hole. How to use a screw extractor will depend on the particular model you’ve chosen, but you’ll likely employ either a wrench or drill to turn the tool counterclockwise. Step 5įinally, insert the tip of your handy screw extractor into the bored hole. Drill about 1/8 to 1/4 inch into the screw head the depth will depend on the size of the screw extractor you’re using. Drill slowly and carefully, making sure to keep the drill and bit aligned straight with the screw. Step 4Īlign the drill bit with the punched spot on the screw head. If the stripped screw is rusted or affixed to metal, place a small drop of penetrating oil on the threads to help loosen its grip. Apply a small drop of thread cutting oil to the head of the broken screw for easier drilling. Select a drill bit that is smaller in diameter than the screw or fastener, and secure it to the power drill.
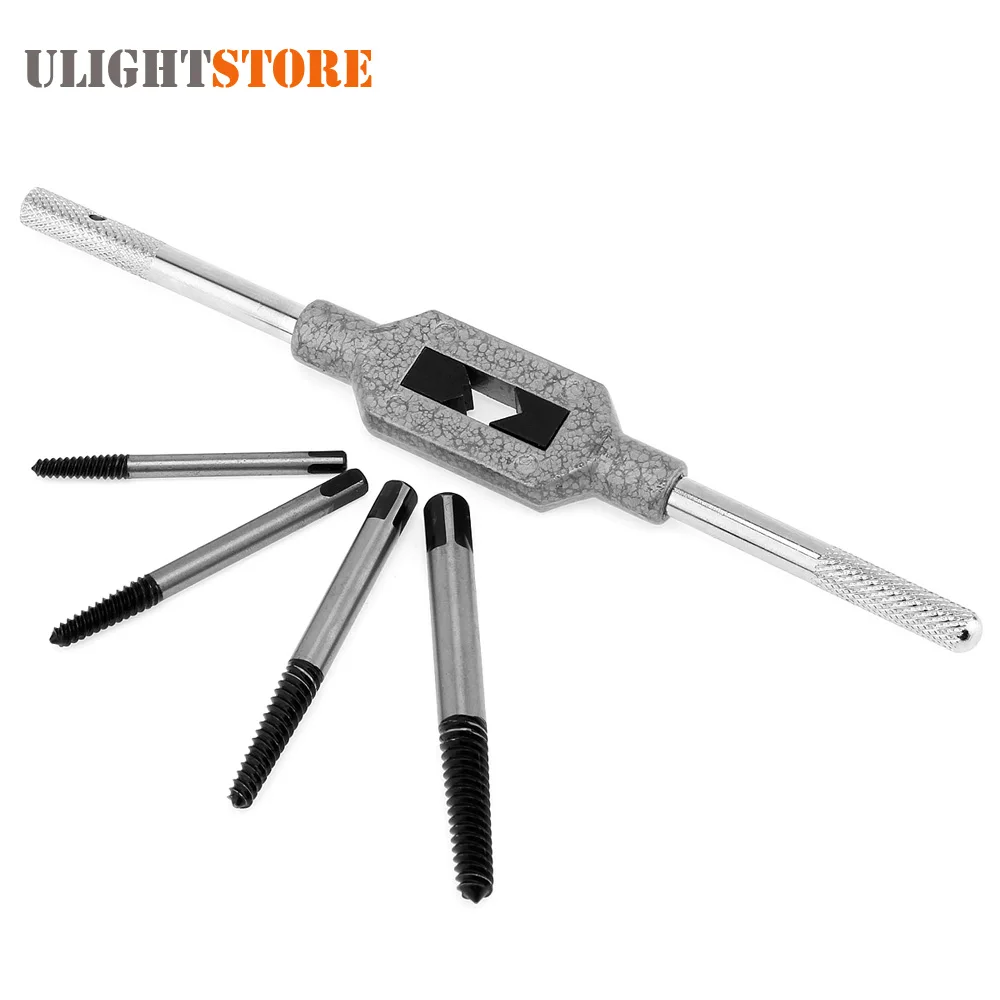
You want to create a small indentation in the center of the screw to help guide the drill bit. Align the center punch with the center of the stripped or broken screw, and lightly strike it with a hammer.
